A bearing is a machine element that supports another moving machine element known as a journal. It enables a relative motion between the contact surfaces of the members while carrying the load. While doing so a certain amount of power is wasted in overcoming frictional resistance due to the relative motion between the contact surfaces. We need to study the types of Bearings, design, and materials used for bearings briefly. In the previous article, we discussed the different types of Bearings. Sliding Contact Bearings are one of the types of bearings depending upon the nature of contact. In this article, let us discuss the Sliding Contact Bearings in detail such as types, materials, and their essential properties.
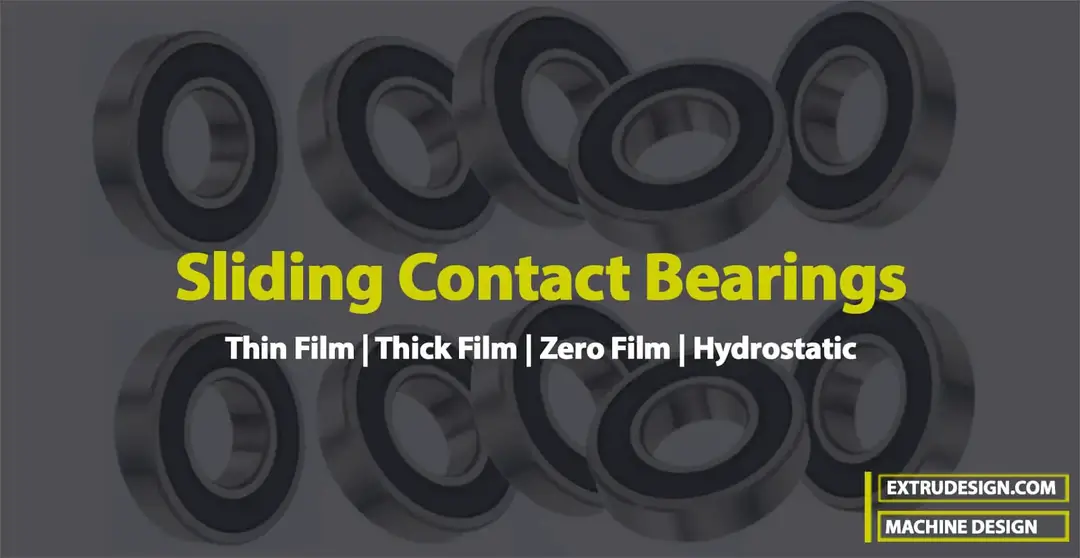
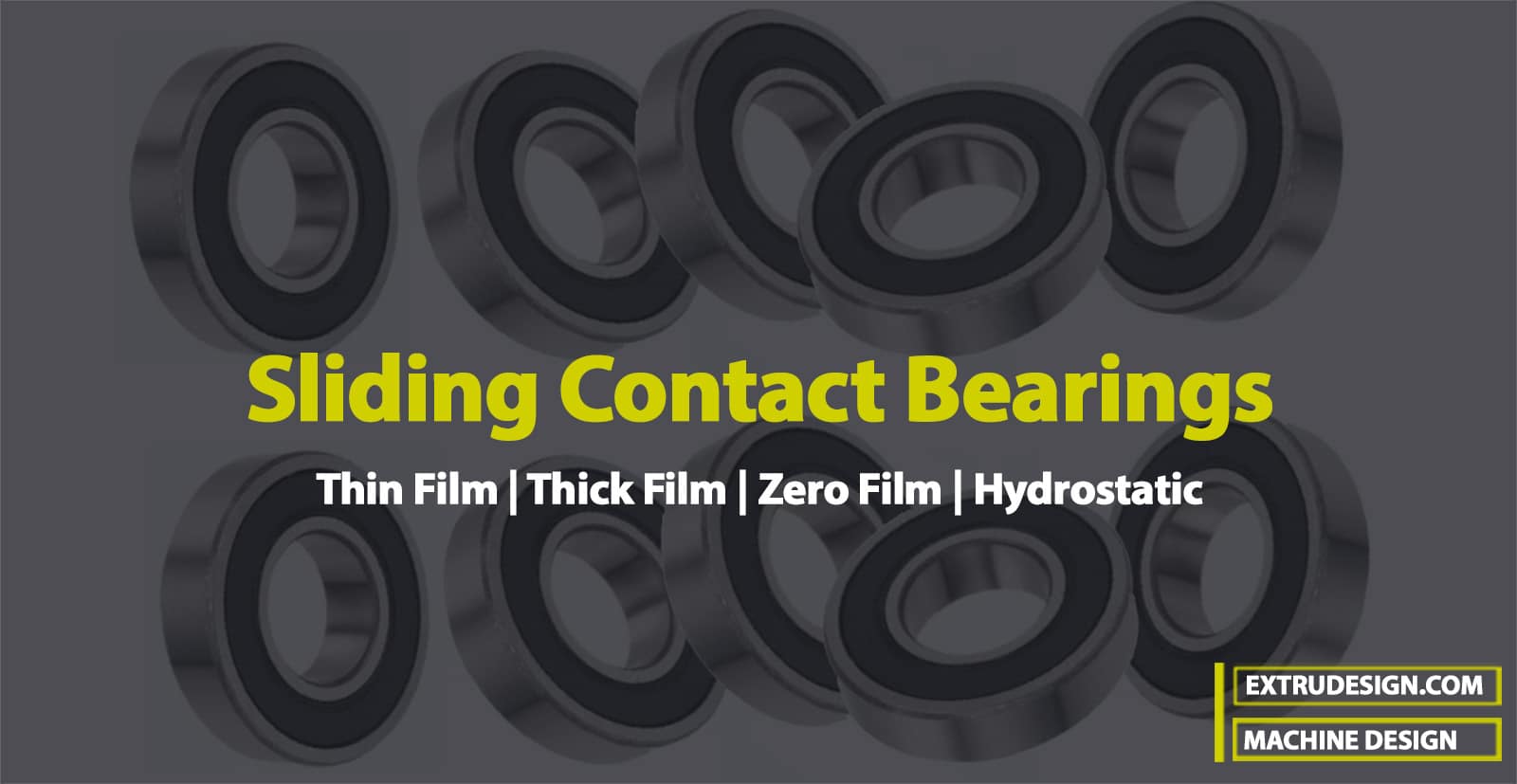
A little consideration will show that a certain amount of power is wasted in overcoming frictional resistance due to the relative motion between the contact surfaces. If the rubbing surfaces are in direct contact, there will be rapid wear. To reduce frictional resistance and wear and in some cases to carry away the heat generated, a layer of fluid known as lubricant may be provided. The lubricant used to separate the journal and bearing is usually a mineral oil refined from petroleum, but vegetable oils, silicon oils, greases, etc., may be used.
Sliding Contact Bearings
The sliding contact bearings in which the sliding action is guided in a straight line and carrying radial loads, as shown in the following figure, may be called slipper or guide bearings. Such types of bearings are usually found in cross-head of steam engines.

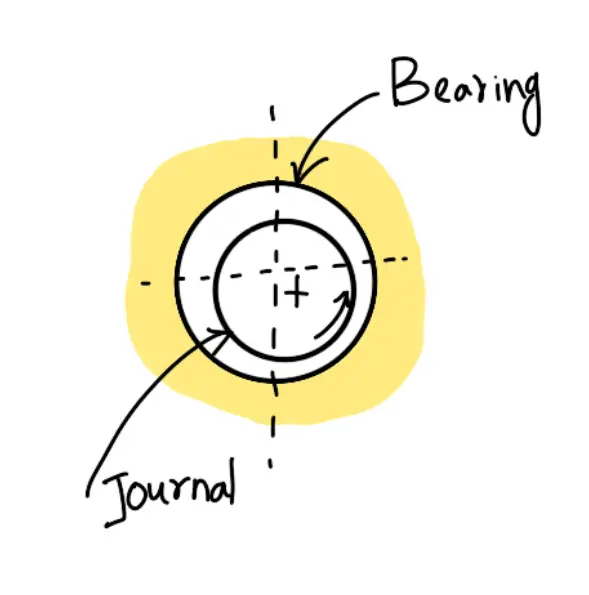
The sliding contact bearings in which the sliding action is along the circumference of a circle or an arc of a circle and carrying radial loads are known as journal or sleeve bearings. When the angle of contact of the bearing with the journal is 360° as shown in the above figure, then the bearing is called a full journal bearing. This type of bearing is commonly used in industrial machinery to accommodate bearing loads in any radial direction.
When the angle of contact of the bearing with the journal is 120°, as shown in the following figure, then the bearing is said to be a partial journal bearing. This type of bearing has less friction than a full journal bearing, but it can be used only where the load is always in one direction. The most common application of the partial journal bearings is found in railroad car axles. The full and partial journal bearings may be called as clearance bearings because the diameter of the journal is less than that of the bearing.

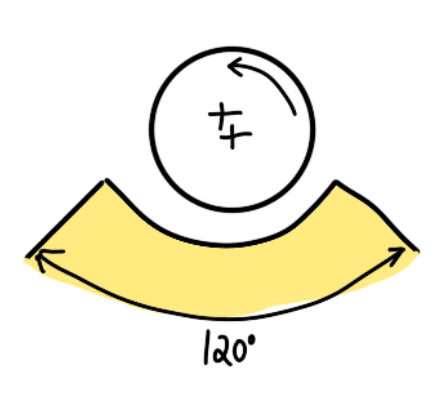
When a partial journal bearing has no clearance i.e. the diameters of the journal and bearing are equal, then the bearing is called a fitted bearing, as shown in the following figure.


Types of Sliding Contact Bearings
The sliding contact bearings, according to the thickness of the layer of the lubricant between the bearing and the journal, may also be classified as follows:
- Thick film bearings: The thick film bearings are those in which the working surfaces are completely separated from each other by the lubricant. Such types of bearings are also called hydrodynamic lubricated bearings.
- Thin film bearings: Thin film bearings are those in which, although lubricant is present, the working surfaces partially contact each other at least part of the time. Such types of bearings are also called boundary-lubricated bearings.
- Zero film bearing: The zero film bearings are those that operate without any lubricant present.
- Hydrostatic or externally pressurized lubricated bearings: Hydrostatic bearings are those that can support steady loads without any relative motion between the journal and the bearing. This is achieved by forcing externally pressurized lubricant between the members.
Hydrodynamic Lubricated Bearings
We have already discussed that in hydrodynamic lubricated bearings, there is a thick film of lubricant between the journal and the bearing. A little consideration will show that when the bearing is supplied with sufficient lubricant, pressure is built up in the clearance space when the journal is rotating about an axis that is eccentric with the bearing axis. The load can be supported by this fluid pressure without any actual contact between the journal and the bearing. The load-carrying ability of a hydrodynamic bearing arises simply because a viscous fluid resists being pushed around. Under the proper conditions, this resistance to motion will develop a pressure distribution in the lubricant film that can support a useful load.
Properties of Sliding Contact Bearing Materials
When the journal and the bearings have proper lubrication i.e. there is a film of clean, non-corrosive lubricant in between, separating the two surfaces in contact, the only requirement of the bearing material is that they should have sufficient strength and rigidity. However, the conditions under which bearings must operate in service are generally far from ideal and thus the other properties as discussed below must be considered in selecting the best material.


1. Compressive strength: The maximum bearing pressure is considerably greater than the average pressure obtained by dividing the load to the projected area. Therefore the bearing material should have high compressive strength to withstand this maximum pressure so as to prevent extrusion or other permanent deformation of the bearing.
2. Fatigue strength: The bearing material should have sufficient fatigue strength so that it can withstand repeated loads without developing surface fatigue cracks. It is of major importance in aircraft and automotive engines.
3. Comfortability: It is the ability of the bearing material to accommodate shaft deflections and bearing inaccuracies by plastic deformation (or creep) without excessive wear and heating.
4. Embeddability: It is the ability of bearing material to accommodate (or embed) small particles of dust, grit, etc., without scoring the material of the journal.
5. Bondability: Many high-capacity bearings are made by bonding one or more thin layers of a bearing material to a high-strength steel shell. Thus, the strength of the bond i.e. bondability is an important consideration in selecting bearing material.
6. Corrosion resistance: The bearing material should not corrode away under the action of lubricating oil. This property is of particular importance in internal- combustion engines where the same oil is used to lubricate the cylinder walls and bearings. In the cylinder, the lubricating oil comes into contact with hot cylinder walls and may oxidize and collect carbon deposits from the walls.
7. Thermal conductivity: The bearing material should be of high thermal conductivity so as to permit the rapid removal of the heat generated by friction.
8. Thermal expansion: The bearing material should have of low coefficient of thermal expansion so that when the bearing operates over a wide range of temperatures, there is no undue change in the clearance.
All these properties as discussed above are, however, difficult to find in any particular bearing material. The various materials are used in practice, depending upon the requirement of the actual service conditions. The choice of material for any application must represent a compromise. The following table shows a comparison of some of the properties of more common metallic-bearing materials.
Bearing material | Tin base Babbit | Comfortability | Embeddability | Anti-scoring | Corrosion resistance | Comfortability |
Lead base Babbit | Poor | Good | Excellent | Excellent | Excellent | Poor |
Lead base babbit | Poor to fair | Good | Good | Good to excellent | Fair to good | Poor |
Lead bronze | Fair | Poor | Poor | Poor | Good | Fair |
Copper lead | Fair | Poor | Poor to fair | Poor to fair | Poor to fair | Fair to good |
Aluminium | Good | Poor to fair | Poor | Good | Excellent | Fair |
Silver | Excellent | Almost none | Poor | Poor | Excellent | Excellent |
Silver lead deposited | Excellent | Excellent | Poor | Fair to good | Excellent | Excellent |
Materials used for Sliding Contact Bearings

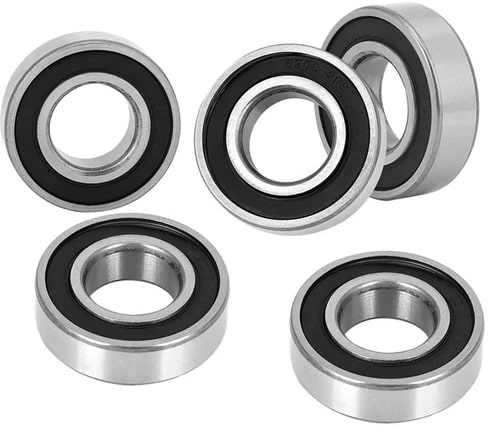
The materials commonly used for sliding contact bearings are discussed below :
1. Babbit Metal:
The tin base and lead base babbitts are widely used as a bearing material because they satisfy most requirements for general applications. The babbits are recommended where the maximum bearing pressure (on the projected area) is not over 7 to 14 N/mm2. When applied in automobiles, the babbit is generally used as a thin layer, 0.05 mm to 0.15 mm thick, bonded to an insert or steel shell. The composition of the babbitt metals is as follows:
Tin base babbits : Tin 90% ; Copper 4.5% ; Antimony 5% ; Lead 0.5%.
Lead base babbits : Lead 84% ; Tin 6% ; Anitmony 9.5% ; Copper 0.5%.
2. Bronzes:
The bronzes (alloys of copper, tin and zinc) are generally used in the form of machined bushes pressed into the shell. The bush may be in one or two pieces. The bronzes commonly used for bearing material are gunmetal and phosphor bronzes.
The gunmetal is used for high-grade bearings subjected to high pressures (not more than 10 N/mm2 of projected area) and high speeds.
The phosphor bronze is used for bearings subjected to very high pressures (not more than 14 N/mm2 of projected area) and speeds.
Gunmetal: Copper 88% ; Tin 10% ; Zinc 2%
phosphor bronze: Copper 80% ; Tin 10% ; Lead 9% ; Phosphorus 1%
3. Cast iron
The cast iron bearings are usually used with steel journals. Such type of bearings are fairly successful where lubrication is adequate and the pressure is limited to 3.5 N/mm2 and speed to 40 metres per minute.
4. Silver
The silver and silver lead bearings are mostly used in aircraft engines where the fatigue strength is the most important consideration.
5. Non-metallic bearings:
The various non-metallic bearings are made of carbon graphite, rubber, wood, and plastics. The carbon-graphite bearings are self-lubricating, dimensionally stable over a wide range of operating conditions, chemically inert, and can operate at higher temperatures than other bearings. Such types of bearings are used in food processing and other equipment where contamination by oil or grease must be prohibited. These bearings are also used in applications where the shaft speed is too low to maintain a hydrodynamic oil film.
The soft rubber bearings are used with water or other low-viscosity lubricants, particularly where sand or other large particles are present. In addition to the high degree of embeddability and conformability, the rubber bearings are excellent for absorbing shock loads and vibrations. The rubber bearings are used mainly on marine propeller shafts, hydraulic turbines, and pumps.
Wood bearings are used in many applications where low cost, cleanliness, inattention to lubrication, and anti-seizing are important.
The commonly used plastic material for bearings is Nylon and Teflon. These materials have many characteristics desirable in bearing materials and both can be used dry i.e. as a zero film bearing. The Nylon is stronger, harder, and more resistant to abrasive wear. It is used for applications in which these properties are important e.g. elevator bearings, cams in telephone dials, etc. The Teflon is rapidly replacing Nylon as a wear surface or liner for journal and other sliding bearings because of the following properties:
- It has a lower coefficient of friction, about 0.04 (dry) as compared to 0.15 for Nylon.
- It can be used at higher temperatures up to about 315°C as compared to 120°C for Nylon.
- It is dimensionally stable because it does not absorb moisture
- It is practically chemically inert.