Force guage, parts, types, specifications, applications
Force guage, parts, types, specifications, applications
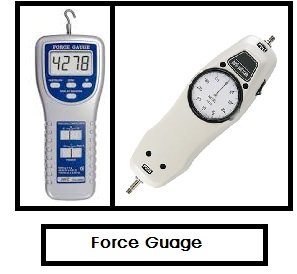
What is a force guage?
These are measuring instruments that measure the amount of force acting on an object during a test or operation. Several industries use them for testing and quality control purposes, including manufacturing. Typically, force sensors are used to perform push or pull tests. force sensor components
Another name?
Force meters are also known as force meters or Newton meters.
Types:
Several types are available, each designed for specific applications and measurement requirements. Here are some common types of force sensors:
Mechanical force sensors: They uses mechanical principles to measure force. They usually have a spring mechanism that deflects in proportion to the force applied. The deflection is then displayed on a dial or scale to indicate the force. These sensors are user-friendly, durable, and often inexpensive. They are often used for basic force measurements in applications such as quality control and tensile/compression testing.
Digital force sensors: They use electronic sensors such as strain gauges to measure force. The force measurement is converted into an electrical signal and displayed digitally on an LCD or LED screen. Digital force sensors offer greater precision, accuracy, and additional functionality than mechanical sensors. They often provide options for data logging, peak hold, statistical analysis, and connection to external devices or software.
Air force sensor: It uses compressed air or gas to measure force. They use a pneumatic system where an applied force compresses the gas and the change in pressure is measured and displayed. Pneumatic pressure gauges are suitable for applications where non-contact force measurement is required or there are concerns about electrical interference or hazardous environments.
Hydraulic force sensor: It uses hydraulic pressure to measure force. They consist of a piston-cylinder system filled with hydraulic fluid. The applied force compresses the fluid and the resulting pressure is measured and displayed. Hydraulic load cells are often used in high-load applications such as heavy engineering, construction, and load testing where high load capacity and durability are important.
Wireless force: Wireless force are digital force sensors that have wireless communication capabilities. They can wirelessly transmit force data to a computer or other compatible device for real-time monitoring, data logging, or analysis. These sensors offer convenience, flexibility, and the ability to perform force measurements in remote or hard-to-reach locations.
Custom load cells: load cells can be customized or specialized depending on specific applications and requirements. This may include modifications to the load cell, fixtures, or fixtures to meet specific test scenarios or unique measurement needs.
Common parts:
Depending on the model and design, the parts of a power metre can differ. However, here are the common components found in most force sensors:
Load Cell: The load cell is an important part of the force sensor. It is responsible for converting the applied force into an electrical signal. Strain gauges are available in different versions, such as strain gauge, capacitive or piezoelectric, and are selected based on the desired measuring range and accuracy.
Display: The force sensor has a display that shows the measured force in selected units. The display can be digital or analog, depending on the model. Digital displays often provide additional functionality such as peak hold, data logging, and statistical analysis.
Enclosure: The enclosure or housing of the meter provides protection and structural support for the internal components. It is usually made of durable materials such as plastic or metal. The design may include ergonomic features to ensure ease of use when measuring force.
Control buttons: Force sensors have control buttons or switches to operate and configure the device. These buttons are used to turn the sensor on/off, select units of measurement, reset the sensor, and access additional functions or settings.
Power Source: Meters can be powered by a variety of sources, including batteries, rechargeable batteries, or AC adapters. The power supply provides the electrical energy required to operate the sensor and power the display.
Calibration Mechanism: Many force sensors have a calibration mechanism or function to ensure accuracy. This can be a calibration button or a port for connecting an external calibration device. Calibration is required to maintain the accuracy of the sensor over time and should be performed regularly.
Accessories: Force sensors often come with accessories to facilitate various measurement tasks. These can be interchangeable devices, fixtures, hooks, or adapters that allow the force sensor to be used for specific test scenarios.
It is important to note that force sensors may have additional features and components depending on the manufacturer and model. For detailed information on a specific force gauge model, it is recommended to refer to the owner's manual or manufacturer's specifications.
Understanding force gauge specifications:
Most force sensors have the following three general characteristics. Please note that the parameters of these devices may vary from manufacturer to manufacturer and the characteristics vary depending on the type of force sensor. Understanding these standards will make it easier to find or develop a model.
Capacity:
Size or capacity is the maximum peak value a device can measure. When choosing a pressure gauge, the measuring range should also be taken into account, as it directly affects the accuracy of the readings
Precision:
Sensor accuracy is the degree to which a device can measure values within a given size or capacitance. For example, if the force sensor is rated at 50 N with an accuracy of ± 2%, the device can measure values between 46 N and 54 N with an error of up to 2%.
High School degree:
High school diploma: "Gradation" is the number of lines on a measurement scale on a gadget.
Authorization:
The degree of accuracy with which a measurement can be made, commonly referred to as resolution, is determined by capacitance and scaling. A resolution of 500/100 means that an analog force transducer of 500 N with 100 divisions has a resolution of 5 N.
Unit:
Analog force transducers are usually pre-programmed with a fixed unit of measure, while digital force gauges allow the user to select from several units.
Confirmation options:
Some force transducers come with different mounting options, while others have a fixed mounting type. Mounting options include mandrels, hooks, plates/adapters, and handles.
Communication interface:
Digital force sensors have an interface that allows the device to be connected to a computer for data analysis and archiving. Common interface types for digital force gauges are USB, RS232, and Bluetooth. Analog force sensors lack this capability because they do not have the internal memory needed to store measurement data. Instead, you must manually record the readings from your analog devices.
Progress or deviation:
Stroke (deflection) is the maximum movement of the plunger used to evaluate push/pull force, usually determined by reading the full gauge.
Application of force gauge:
1)Pinch testing is a common application for force sensors. This type of test is used to determine the compressive strength of materials such as concrete, metal, wood, and plastics. The test involves applying a force to a sample until it breaks or deforms. The maximum force applied to the material is then recorded.
2)Professional boxers use it to measure the power of their punches. You can use the results of these tests to help athletes train more effectively and improve their performance.
3)In the automotive industry, force sensors test the strength of car parts and components such as springs, shock absorbers, and seats. These tests ensure that these components can withstand the stresses to which they are subjected during normal use.
4)Mechanical spring manufacturers use force sensors to evaluate the strength and durability of their products. This is to ensure that the springs work properly and do not break as designed.
5)Gauges are used to test the strength of materials to ensure they are suitable for their intended use. It is an important aspect of various industries, including construction, automotive, and manufacturing.
6)During the design process, designers and engineers use force sensors to determine the carrying capacity of prototypes. This allows changes to be made to the product before it goes into mass production.
Force sensors are often used to test the strength and durability of materials and to evaluate the performance of mechanical springs. In addition, they are often used in the design process of new products to ensure they can withstand the forces they will experience in the real world.
What's Your Reaction?
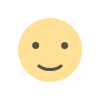
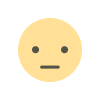
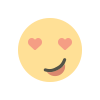
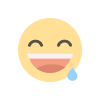
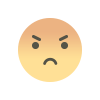
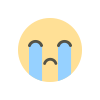
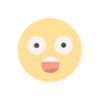