Laser Doppler Vibrometer, Principle, Types
Laser Doppler vibrometry measures motion and velocity in fields like science, engineering, and acoustics using high resolution and linear amplitude.
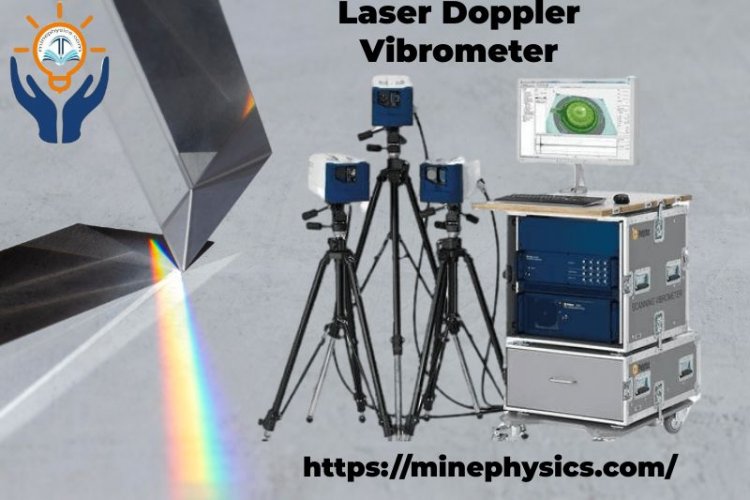
Laser Doppler Vibrometry:
It is currently the method that provides the best resolution for motion and velocity and is used in many areas of basic science. It provides femtometer amplitude resolution, is linear, and therefore has a constant amplitude to very high-frequency ranges, currently reaching practically above 2 GHz. These properties do not depend on the measurement distance, so this principle is used in both microscopic operations and very large distances. Light as a sensor does not affect the sample, making it non-invasive and therefore allowing measurements on very small and very light structures. Because this process has such unsurpassed properties, Polytec has made it reliable and suitable for both laboratory and outdoor use.
Principle:
The working principle is based on the Doppler effect of scattered light from micron-sized tracer particles that move together with the fluid. Two beams of light are required to measure each velocity component.
Working:
The vibrometer is typically a two-beam laser interferometer that measures the difference in frequency (or phase) between an internal reference beam and a test beam. The most common type of laser in LDV is the HeNe laser, although diode lasers, fiber lasers, and Nd: YAG lasers are also used. The test beam is aimed at the target and scattered light from the target is collected and interferes with the reference beam on a photodetector, usually a photodiode. Most commercial vibrometers operate in heterodyne mode, adding a known frequency offset (usually 30-40 MHz) to one of the beams. This frequency shift is usually generated by a Bragg cell or an acoustic-optic modulator.
The laser beam, with a frequency fo, is divided into a reference beam and a test beam by means of a beam splitter. The test beam then passes through a Bragg cell which adds a frequency shift fb. This frequency-shifted beam is then aimed at the target. fd = 2*v(t)*cos(θ), where v(t) is the target's velocity as a function of time, is the angle formed by the laser beam and the target's velocity vector, and is the light's wavelength, describes the Doppler shift that the target introduces into the beam.
Light is scattered in all directions by the target, but some of the light is captured by the LDV and reflected back to the photodetector by the beamsplitter. This light has a frequency of fo + fb + fd. This scattered light is combined with the reference beam of the photodetector. The laser start frequency is very high (> 1014 Hz ), higher than the detector response. However, the detector responds to a beat frequency between the two beams, namely fb + fd (usually in the tens of MHz range). The frequency of the Bragg cell serves as the carrier frequency and the frequency of the Doppler shift serves as the modulation frequency of the FM signal produced by the photodetector. This signal can be demodulated to obtain the velocity versus time of the vibrating target.
Who Invented?
The Scanning Laser Vibrometer or Scanning Laser Doppler Vibrometer was first developed by British loudspeaker company Celestion around 1979, further developed in the 1980s, and marketed around 1986 by Ometron, Ltd.
Types:
There are different types, each with its own configuration and application. Here are some common types:
Single Point LDV: This is the simplest type and measures the vibration of a single point on an object. It uses a single laser beam and photodetector to detect the frequency shift caused by an object's motion. Single-point LVs are widely used for general vibration measurement and modal analysis.
Scanning: Unlike single-point, scanning LDVs are capable of measuring vibration over a larger area or the entire surface of an object. They use a combination of scanning mirrors and position-sensitive detectors to quickly scan the surface of an object with a laser beam, measuring speed or movement at any spot. LDV scanning is useful for generating vibration maps and defining vibration patterns of structures.
Heterodyning LDV: It uses a technique called heterodyning, where the frequency of scattered light is mixed with a reference frequency before it is detected. By using a separate reference beam and adjusting the frequency difference, it can improve measurement accuracy and improve the signal-to-noise ratio.
Fiber Optic: It uses optical fibers to deliver and collect the laser beam, enabling remote measurement and access to confined spaces. They provide flexibility in sensor head placement and are often used in industrial applications such as vibration monitoring in rotating equipment or vibration measurement in hazardous areas.
Auto-Mixing: They are a compact and economical version. In this configuration, the laser diode used to emit the laser beam also acts as a photodetector. The scattered light reflected in the laser diode interferes with the laser radiation itself, modulating the laser output intensity. By analyzing this modulation, auto-mixing LDVs can measure vibrations. They are often used to measure displacement in applications such as precise positioning or tracking human body movements.
Applications:
Vibrometers have a wide variety of applications in various fields. Here are some key uses:
Structural Dynamics and Modal Analysis: LOSs are widely used in structural engineering and civil engineering to measure vibration and analyze the dynamic behavior of structures. They can determine natural frequencies, waveforms, and damping characteristics to help evaluate structural integrity and optimize designs.
Non-destructive Testing (NDT): LDVs are valuable tools for non-destructive testing where they can detect and evaluate defects or imperfections in structures or materials by analyzing the vibrations they produce. This application is especially useful for quality control in manufacturing industries such as aerospace, automotive, and construction.
Acoustic Analysis: LDV can be used to analyze sound waves and vibrations in audio systems, musical instruments, and environmental noise. They can measure the vibrations of diaphragms, speaker cones, and other acoustic components and provide information about sound quality, resonant frequencies, and structural integrity.
Biomechanics and Human Motion Analysis: LDVs are used in biomechanical research to measure vibrations and displacements of parts of the human body during various activities. They can help analyze the mechanisms of human movement, study gait analysis, evaluate the effectiveness of prosthetics, and contribute to sports science and rehabilitation research.
Micro/nanotechnology: LDVs are valuable tools for the characterization of micro- and nano-scale devices, such as micro-electro-mechanical systems (MEMS) and nano-scale actuators. They can measure small structures' motion, displacement, and resonance frequencies, aiding in the design and quality control of miniature devices.
Automotive and Aerospace: LDVs play a vital role in vehicle and aircraft development and testing. They can measure vibrations in engines, suspension systems, and airframes, helping engineers optimize performance, improve ride comfort and identify potential failures or fatigue issues.
Vibration Isolation and Control: LDVs are used in active vibration control systems to measure and monitor vibrations in real-time. By providing accurate feedback on vibration levels, LDVs can ensure that active control systems are fine-tuned to minimize unwanted vibration, improve stability and improve the performance of structures and equipment.
What's Your Reaction?
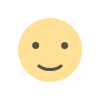
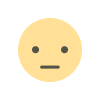
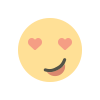
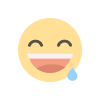
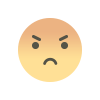
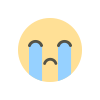
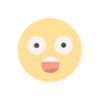