What is screw guage?
What is screw guage?
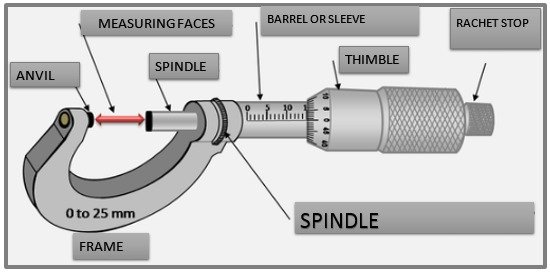
What is screw guage?
A micrometer, also known as a micrometer micrometer or simply a micrometer, is a precision measuring instrument used to measure the diameter or thickness of objects with high accuracy.
Components of screw guage:
The main components of a screw pressure gauge are:
Frame:
The frame is a C-shaped structure that contains the other components of the micrometer. Provides stability and support during measurements.
Anvil: The anvil is the stationary end of a micrometer, usually on the side of the frame. It has a flat or rounded surface on which the object to be measured is placed.
Spindle: The spindle is the moving part of the micrometer that slides on the frame. It has threads that grip in a thimble for precise movement and measurement.
Thimble: The thimble is attached to the chuck and provides a rotating mechanism to move the chuck. It has markings or graduations on its surface to indicate the distance the spindle travels.
Sleeve: The sleeve is a cylindrical component that houses the spindle and provides a guide for its movement. Usually a linear scale is applied to the surface that allows direct measurement of the distance traveled by the spindle.
Ratchet stop:
Some screw gauges have a ratchet stop mechanism. Provides constant and controlled pressure on the object to be measured, preventing excessive force that could interfere with the measurement.
Locking mechanism: Screw-in gauges often have a locking mechanism, such as a knurled locknut or friction sleeve, to lock the chuck in place and prevent accidental movement.
Vernier scale (optional): Some modern screw gauges have a vernier scale on the sleeve or thimble. Provides additional subdivisions for more accurate measurements, improving measurement resolution.
Working procedure:
Zeroing:
The screw gauge must be zeroed or calibrated before measurement. This is done by bringing the anvil and mandrel into contact and turning the sleeve until the scale on the hub aligns with zero on the sleeve.
Measurement:
To measure the thickness or diameter of an object, an anvil is placed against one end of the object and the mandrel is slowly rotated with a thimble. The mandrel moves towards the object and the user rotates the thimble until the object is held firmly between the anvil and the mandrel.
Reading:
The measurement is taken from the linear scale on the sleeve and the dial on the thimble. The linear scale on the sleeve indicates whole units, while the dial on the thimble indicates fractional units or a more accurate measurement. The linear scale readings are added to the fractional scale readings to obtain the final measurement.
Calculation:
The size reading is calculated by adding the whole value of the unit of measure on the main scale to the portion that is read on the thimble scale. Each division on the thimble scale represents a fraction of the tone, allowing for accurate measurements.
Accuracy:
The accuracy of a screw gauge depends on the pitch and the number of divisions on the thimble scale. The high-quality measuring screw can measure distance or thickness with sub-micron accuracy.
These components work together to measure the size of objects with high precision. By rotating the drum and observing the linear scale and markings, the user can determine the distance the spindle has traveled, allowing for accurate measurements.
Least count:
The minimum value (least count) of a screw gauge, also known as a micrometer screw gauge, depends on the pitch of the screw and the number of divisions on the dial. Formula for calculating the minimum number of screw gauges:
Least count = step / number of divisions on the dial
Pitch refers to the distance a screw travels when it completes one full revolution. The number of divisions on the round scale corresponds to the number of evenly spaced divisions on the round scale of the screw caliber.
Usually, the micrometer has a pitch of 0.5 mm and a circular scale with 100 divisions. By using these values in a formula, we can calculate the minimum amount as follows:
L.C = 0.5 mm / 100 parts
= 0.005mm
Therefore, the smallest reading of a standard screw-in caliper with a 0.5 mm pitch and a 100-division dial is 0.005 mm or 5 micrometers (µm).
Zero error:
In the context of a screw gauge, "zero error" refers to a shift or discrepancy in the instrument's readings when the measuring surfaces are not in contact with an object. Ideally, there should be no reading on the dial when the screw-in caliber is at zero.
Types of zero error:
There are two types of zero error in a screw gauge:
Positive Zero Error:
Occurs when the zero mark on the dial is above the reference line or zero line. In other words, the sensor displays a positive value even in the absence of a measured object. To obtain a correct measurement, this error value must be subtracted from the readings obtained when measuring the object.
Negative Zero Error:
Occurs when the zero mark on the dial is below the reference line. In this case, the sensor shows a negative value when the object is missing. To obtain accurate measurements, this error value must be added to the readings obtained when measuring the object.
Zero correction:
To determine the null error, you can follow these steps:
Close the jaws of the micrometer so that no objects are trapped.
Check the position of the zero mark on the dial relative to the baseline.
If it is above the control line, it indicates a positive zero error.
If it is below the baseline, it indicates a negative zero error.
Record the zero error value.
When you measure an object, you add or subtract zero errors from the measurement value, depending on whether it is positive or negative.
To get accurate results, it is important to account for zero errors when measuring with a screw gauge.
Applications of screw guage:
Here are some common uses for the screw gauge:
Machine building and manufacturing:
Screw gauges are widely used in mechanical engineering and manufacturing to measure the thickness or diameter of various components. They provide accurate measurements of parts such as screws, bolts, nuts and other small mechanical components.
Machining and Metalworking:
Micrometers are a valuable tool for machinists and blacksmiths. They can measure the thickness of materials such as sheet metal or plate to ensure accurate machining and achieve the required tolerances.
Quality control and verification: In industries where accuracy is critical, such as automotive, aerospace or electronics, screw gauges are used for quality control and verification. They help measure critical dimensions and ensure products meet required specifications and standards.
Laboratory and Scientific Research: In scientific laboratories, screw gauges are used to accurately measure small objects or samples. They are used in various fields such as physics, materials science, chemistry and biology to measure sample size, film thickness or other small quantities.
Watchmaking and jewelry: Screw-in calipers are used in watchmaking, jewelry and gemology. They are used to measure the thickness of watch components, gemstones and precious metals with high accuracy.
Carpentry and joinery: In carpentry and joinery, screw gauges are used to measure the thickness of wood, veneer or other materials. They help to accurately cut, hammer or assemble various woodworking components.
Plumbing and Fittings: Pressure gauges can be used to measure the diameter or thickness of pipes, fittings or plumbing components. This helps select the correct parts for installation or repair.
It is worth noting that the application of the screw gauges is not limited to the areas indicated and they can be used wherever precise and accurate measurements of small dimensions are required.
What's Your Reaction?
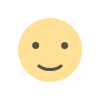
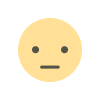
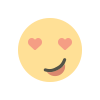
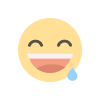
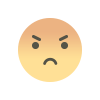
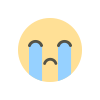
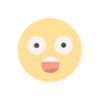